METALS
Machining
Excelling in metals
Operating out of a state-of-the-art, 70,000-square-foot, FDA-registered, ISO 13485:2016 facility in Colorado Springs, EPTAM Precision Metals has specialized in medical implants, external fixation, and instrumentation since its founding in 1982.
This division features resources that leading medical-device companies rely on, including a Class 7 clean room, automated inspection, and a validated supply chain, as well as a dedicated R&D cell. On the shop floor, the precision machining includes 3-, 4-, and 5-axis CNC milling, gun drilling, water jet cutting, Swiss and Super-Swiss machining, and EDM machining.
EPTAM Precision Metals can handle all of its customers’ assembly, packaging, DFM, PPAP, IQ, OQ, and PQ needs. The center’s materials selection list includes titanium, aluminum, and stainless steels such as 17-4, 303, 304, 316, 455, 465, MP35N, Nitronic 60, and BioDur. We work with our customers to source their specific material needs.
Differentiated technology
Unique process and capabilities
3-axis, 4-axis, and 5-axis CNC machining.
Gun drilling, water jet cutting, swiss machining.
EDM (Electrical Discharge Machining)
Automated inspection.
Class 7 clean room.
Small and large production runs.
Compliance with industry standards and regulations.
High precision and accuracy for each product.
3D printing metal.
Some of our work
Materials
Materials offer a wide range of characteristics, and EPTAM’s team of engineers and DFM specialists understand how to select and work with the proper materials. EPTAM recognizes the need for speed to market, deliverability, and supply-chain management. Fortunately, for many EPTAM customers, EPTAM’s market position and size help meet these constantly changing demands.
Stainless steels, including:
17-4
303
304
316
455
465
MP35N
Nitronic 60
Biodur
Equipment
As the leader in complex multi-axis metal machining, EPTAM Precision Metals offers 3, 4, and 5-axis machining centers. We also offer the ultimate and most capable Swiss turn / milling multifunction turning center on the market today. Time-tested sliding headstock technology and Tsugami precision allow us to machine long, slender parts that traditional turning centers cannot. Milling capability from the tool spindle gives us the capability to make virtually any complex part. The ATC and 16-station turret combine to eliminate set-ups and changeovers, making this multi-function the perfect choice for short runs of complex parts ensuring that we can handle any project with precision and accuracy.
Swiss machining
- 5, 6, 8, 11, or 12 simultaneous axis.
- Simultaneous turning and drilling.
- Machining with up to 4 tools working simultaneously.
- Enhanced synchronized superimposed operation.
- Up to 22 tools for main and sub-spindle work.
- Rotating and synchronized guide bushings.
- Up to 16,000 RPM main spindle.
Swiss turn mill
- Swiss turn benefits: multitasking flexibility. Sliding headstock technology enables precision machining of long, slender parts that are impossible to produce on conventional turning centers. This is coupled with an automatic tool changer (ATC) and 16-station turret, providing additional flexibility.
- Identically powered main/sub spindles with independent 11/7.5 kW motors, plus 10,000 RPM tool spindle speed.
- The unique Tsugami "dual spindle" structure maintains superior gripping power and workpiece accuracy.
- 16-station turret for flexible tool storage.
- 60-tool automatic tool changer (ATC) for additional storage and flexibility. Milling/turning tools share the same type of shank. Enhanced milling capability with a horizontal tool spindle mounted to the B-axis. Controlled by a Fanuc 32i-B control.
Swiss machining
- 5, 6, 8, 11, or 12 simultaneous axis.
- Simultaneous turning and drilling.
- Machining with up to 4 tools working simultaneously.
- Enhanced synchronized superimposed operation.
- Up to 22 tools for main and sub-spindle work.
- Rotating and synchronized guide bushings.
- Up to 16,000 RPM main spindle.
Swiss turn mill
- Swiss turn benefits: multitasking flexibility. Sliding headstock technology enables precision machining of long, slender parts that are impossible to produce on conventional turning centers. This is coupled with an automatic tool changer (ATC) and 16-station turret, providing additional flexibility.
- Identically powered main/sub spindles with independent 11/7.5 kW motors, plus 10,000 RPM tool spindle speed.
- The unique Tsugami "dual spindle" structure maintains superior gripping power and workpiece accuracy.
- 16-station turret for flexible tool storage.
- 60-tool automatic tool changer (ATC) for additional storage and flexibility. Milling/turning tools share the same type of shank. Enhanced milling capability with a horizontal tool spindle mounted to the B-axis. Controlled by a Fanuc 32i-B control.
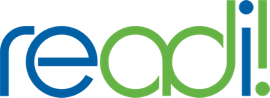
Rapid Prototyping
Every EPTAM client faces the same challenges – design parts to meet performance standards and ensure production ramp and capacity availability while controlling costs.