MOLDING
Silicone
Excelling in molding silicone
Since 2005, EPTAM has been a vertically integrated injection molding solutions partner in the medical/healthcare, industrial, consumer, and defense industries. We support the entire product lifecycle, with rapid prototyping, tool development, validation, production molding, and value-added operations. Our team consists of experienced engineers, technicians, operators, and quality managers that have experience with materials, tooling, molding, and assembly of silicone and thermoplastic, assembly material, and molding.
EPTAM offers a collaborative approach to servicing our silicone rubber and thermoplastic customers by combining our capabilities and expertise with understanding your specific design, engineering, and manufacturing needs. EPTAM provides progressive manufacturing solutions such as micro-molding, multi-material, and insert molding. Our scalability ensures objectives are met on time, whether it’s the design and development of a new product or immediate full-scale, high-volume production needs.
Some of our work
Differentiated technology
Unique process and capabilities
- Experienced project, plastic, quality, and tooling engineers. Leverage years of mold building and processing experience to support new and growing projects.
- EPTAM Plastic MA and EPTAM Silicone use state of the art molding equipment and automation to support.
- Maintain new equipment - Engel and Arburg injection machines.
- Wide range of thermoplastic engineering grade resins such as: PC, PS, and TPE .
- High-performance materials such as PEEK and PMMA.
Liquid silicone rubber (LSR)
- Compression molding
- Injection molding
- High-performance materials such as PEEK and PMMA.
- Wide range of LSR grades from virtually all major manufacturers.
- Compression molding
- Injection molding
- Experience from low to high durometer
- Optical, colored, etc.
- Self-bonding/adhesive grades
- Overmolding to metals, thermoplastics, other silicones, etc.
- In-house silicone prototype and production mold building capabilities
Secondary processes
- Automated assembly
- Heat staking
- Ultrasonic welding
- Pad printing
- Slitting
Our quality system
- ISO 13485:2016 registered Albright Silicone division location
- ISO 9001:2015 registered
- Total cost of non-quality of less than 1% and improving
- IQMS™ ERP system
- SPC monitoring
- 8D problem-solving methodology
- ISO Class 8 certified cleanrooms
- Cutting-edge metrology technology with fully programmable touch probe CMM vision systems
Equipment
EPTAM offers fully validated molding processes and state-of-the-art equipment to ensure the highest level of precision, and all products are manufactured according to our ISO13485 registered Quality Management System. Quality is integrated into every aspect of our company. All procures are developed according to the most rigorous and demanding industry standards.
Plastic Injection – up to 200 tons, shot weight ranging from fraction of an ounce up to 13 ounces
- Up to 200 tons.
- Shot weight ranging from a fraction of an ounce up to 13 ounces.
- Insert and over molding using exotic thermoplastic materials.
- Work with the tightest of tolerances.
CNC 3-Axis, 4-Axis Milling
- CNC 3-axis milling produces precise, accurate, and consistent shapes and sizes
- CNC 4-axis milling allows for machining of complex geometries and improves precision.
- 4-axis milling enables accurate, consistent, and precise control for more complex parts.
CNC 5-Axis, 7-Axis, and Multi-Axis Plastics Machining
- Multus B300 7-Axis Mill / Turn Center Single-Step Operation.
- MU-400 vertical machining delivers complex machined geometries, blending, undercuts, and difficult angles - all in a single setup.
Facilities
EPTAM is equipped with 29 injection molding machines. Production molding machines are 2 years old on average.
EPTAM Lancaster, MA facility
EPTAM’s Lancaster, MA facility is a completely controlled environment, with a recently expanded ISO Class 8 cleanroom. Capabilities include a wide range of press tonnage—28-550 ton with plans to expand—and are committed to continuous reinvestment in operations, with $2 million recently invested in upgrading our cleanroom and purchasing new machines.
EPTAM Leominster, MA facility
EPTAM’s Leominster, MA facility boasts a fully controlled environment with two certified ISO Class 8 clean rooms, one for thermoplastic and one for silicone. We have a diverse range of injection machines, including LSR machines with a capacity ranging from 14 to 120 Tons, and Thermoplastic machines with a capacity of 50 to over 200 Tons. This facility has separate compression room space and is designed to allow for future expansion of equipment or automated assembly cells. Our expertise also includes over-molding silicone onto various materials such as metals, plastics, mesh screens, and other silicones. We have extensive knowledge in LSR injection.
EPTAM is committed to meeting customer scalability requirements. When any single piece of equipment reaches 70% capacity, an additional machine is ordered.
EPTAM Silicone is equipped with LSR injection molding machines ranging from 14-120 ton and compression presses ranging from 10-100 tons. Additionally, we have thermoplastic injection machines ranging from 50-130+ tons with allocated space for additional equipment and capacity. Albright offers prototyping and production tooling with the ability to build a wide range of tooling in house. This is supported by Brother and Topper CNC machines.
Our history
Since 2005, EPTAM has been a vertically integrated injection molding solutions partner in the medical/healthcare, industrial, consumer, and defense industries. We support the entire product lifecycle, with rapid prototyping, tool development, validation, production molding, and value-added operations.
Our team consists of experienced engineers, technicians, operators, and quality managers that have experience with materials, tooling, molding, and assembly of silicone and thermoplastic, assembly material, and molding.
EPTAM offers a collaborative approach to servicing our silicone rubber and thermoplastic customers by combining our capabilities and expertise with understanding your specific design, engineering, and manufacturing needs.
EPTAM provides progressive manufacturing solutions such as micro-molding, multi-material, and insert molding. Our scalability ensures objectives are met on time, whether it’s the design and development of a new product or immediate full-scale, high-volume production needs.
"Our team of highly-talented machinists and engineers deliver value to our customers through early participation in R&D efforts, accelerating new product launches, and resolving complex challenges with agile versatility. It’s why ‘Rapid’ is in our name."
Andrew Igl
Get a Quote
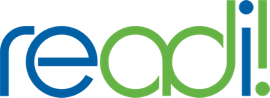
Rapid Prototyping
Every EPTAM client faces the same challenges – design parts to meet performance standards and ensure production ramp and capacity availability while controlling costs.