Metal Injection Molding
(MIM) Capabilities
EPTAM is your Metal Injection Molding Expert
EPTAM Precision is your trusted partner for Metal Injection Molding (MIM), a revolutionary technology that bridges the gap between the design flexibility of plastic injection molding and the strength of metal. Our MIM process enables the production of highly detailed, complex parts with unparalleled precision and efficiency, ideal for a wide range of industries.
Key Advantages
Metal Injection Molding (MIM) combines the design freedom of plastic injection molding with the strength and durability of metals. EPTAM has been perfecting the MIM process for decades, leveraging the latest technology and developing proprietary knowledge to deliver unmatched precision and performance. MIM is the ideal solution for manufacturing small, intricate components at high volumes:
Complex Geometries
Achieve intricate shapes and details that are a challenge with traditional metalworking methods.
Material Versatility
Utilize a wide range of metals, including stainless steel, titanium, and cobalt-chrome.
Scalability
Ideal for high-volume production runs, ensuring consistency and repeatability.
Versatile Integration
MIM components are easily joined or brazed into larger assemblies, providing seamless integration and enhancing the structural integrity and functionality of the final product.
Dedicated MIM R&D Center
Quick turn MUD based molds for development or short run designs, onsite metallurgical lab, Tooling design, DFM services, on site sintering and molding to dial in processes
MIM for Medical Instruments
Metal Injection Molding has revolutionized the production of medical instruments by offering unmatched precision, strength, and reliability. At EPTAM, we specialize in creating intricate components that meet the rigorous demands of the medical industry. Our solutions include:
Surgical Tools
High-precision instruments designed for minimally invasive procedures.
Orthopedic Devices
Durable and biocompatible components for implants and surgical disposable instruments.
Diagnostic Equipment
Complex parts for cutting-edge molecular and clinical diagnostic tools.
Custom Solutions
Tailored designs to meet unique specifications and compliance with stringent regulatory standards.
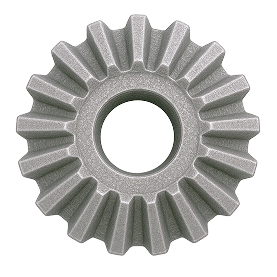
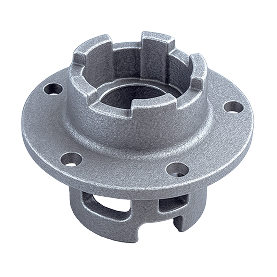
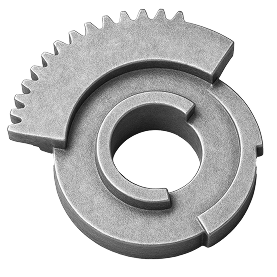
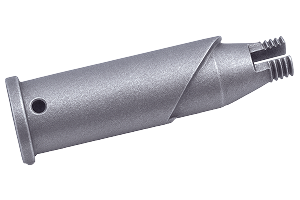
EPTAM’s Investment
EPTAM has made strategic investments in advanced Metal Injection Molding (MIM) technologies, process controls, and specialized talent to support the future of medical manufacturing. Our state-of-the-art equipment and validated systems enable us to produce complex, high-precision components with consistency and scalability. These capabilities are tailored to meet the demands of OEMs in regulated sectors like orthopedic and minimally invasive surgery. Every investment reinforces our commitment to precision, performance, and innovation.
Leading Technology and Expertise
EPTAM’s state-of-the-art facilities and experienced team ensure we deliver top-tier MIM solutions tailored to your unique requirements.
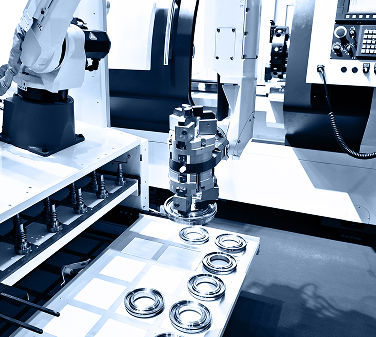
Our Capabilities Include:
- Advanced Molding Equipment
- Custom Tooling
- Material Expertise
- Post-Processing
- Quality Assurance

Our Process
Metal injection molding (MIM) is a metalworking process in which finely-powdered metal is mixed with binder material to create a “feedstock” that is then shaped and solidified using injection molding. The molding process allows for high volume, complex parts to be shaped in a single step. After molding, the part undergoes conditioning operations to remove the binder (debinding) and densify the powders into solid metal (sintering). Finished products are typically small complex shape components under 20 grams in weight and less than .125 maximum wall thickness.
Materials
Materials offer a wide range of characteristics, and EPTAM’s team of engineers and DFM specialists understand how to select and work with the proper materials. EPTAM recognizes the need for speed to market, deliverability, and supply-chain management. Fortunately, for many EPTAM customers, EPTAM’s market position and size help meet these constantly changing demands.
- SS 17-4
- SS 303
- SS 304
- SS 316
- SS MP35N
Understanding Density Profiles in MIM
Gain deeper insights into the role of density profiles in Metal Injection Molding and how they influence part performance and quality. Download our comprehensive whitepaper to explore:
- Real-world applications and benefits of precise density control.
- Methods for optimizing density profiles during production.
- The science behind density distribution in MIM parts.
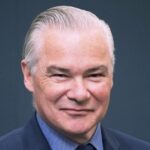
“Lorem ipsum dolor sit amet, consectetur adipiscing elit. Nullam venenatis magna id diam semper, vitae posuere nulla efficitur. Nunc non convallis felis. Sed nec porttitor sem. Quisque nec erat venenatis, semper ex ac, aliquet neque. Pellentesque egestas tellus ac”
Mark Ward
Partner with EPTAM
EPTAM is committed to providing full-service solutions, from prototyping to large-scale production. Our dedicated engineering team offers technical assistance during and after production, ensuring a seamless experience and long-term reliability for your projects.
- Integrated Solutions: End-to-end support from process design to final production.
- Cutting-Edge Innovation: Continually investing in the latest MIM advancements.
- Experienced Team: Decades of expertise in advanced manufacturing technologies.
- Customer Focus: Tailored solutions to meet your specific needs.