PLASTICS
Machining
Excelling in plastics
Since its founding in 1981, EPTAM Plastics, a Northfield, New Hampshire-based company, has been a leader in solving the most difficult challenges in plastic component manufacturing and CNC machining. EPTAM Plastics is the largest North American manufacturer of machined plastic products and assemblies. The professional team comprises over 285 engineers, production specialists, and dedicated quality control experts.
The newly expanded campus in Northfield, New Hampshire, is over 100,000 square feet and has a diverse fleet of dedicated CNC equipment for plastic components. EPTAM’s sales, engineering, manufacturing, and quality teams operate as an extension of the OEM’s design and material engineering departments to establish solutions and specifications for a wide variety of precision-machining applications. With a proven record of providing the highest-quality, tightest-tolerance machined parts for mission-critical applications, the company serves OEM leaders in the Medical Device, BioPharma, Robotic-Assisted Surgeries, Semiconductor, and Aerospace/Defense industries, providing advanced solutions for emerging commercial technologies.
The FDA-registered, ISO 13485:2016 center also features comprehensive automated inspection. With 10+ probe and vision coordinate-measuring machines (CMM), EPTAM Plastics can support you with metal-to-plastic conversions, material design support, and design for manufacturability using FMEA practice. EPTAM Plastics is the leader in complex multi-axis plastic machining using 3-, 5-, and 7-axis machine centers, CNC turning, Swiss, milling, routing, sawing, and drilling. We believe that the key to your success is combining world-class machining with our world-class metrology. We can demonstrate that your geometry is compliant with your intended design and prove it.
Some of our work
Differentiated technology
Unique process and capabilities
Design for manufacturability (DFM) and new product introduction (NPI) processes for assured success.
Machining experience with 500+ unique polymers from rods, sheet and near net blanks.
Material selection assistance and direct purchase from the strategic stock shape suppliers to support your project.
Rough Cut capacity planning model enabling finite and infinite capacity molding.
Geometric dimension and tolerancing (GDT) & coordinate-measure machines CMM’s experts.
In-house automation build and design.
Climate controlled.
3D Printing – BinderJet/FDM/SLS 3D printing metals and plastics.
Assembly pack and clean, including complex assemblies with hundreds of components.
Materials
Materials offer a wide range of characteristics, and EPTAM’s team of engineers and DFM specialists understand how to select and work with the proper materials. EPTAM recognizes the need for speed to market, deliverability, and supply-chain management. Fortunately, for many EPTAM customers, EPTAM’s market position and size help meet these constantly changing demands.
Acetals
Aluminum
Carbon Fiber PEEK
Polysulfone
Propylux® HS2
PPSU
Radel® R5500
SS 17-4
SS 303
SS 304
SS 316
SS MP35N
SS Nitronic 60
SS Biodur
Titanium
UHMW-PE – Implantable
Ultem (Colored)
60% Woven CF PEEK
Equipment
As the leader in complex multi-axis plastic machining, EPTAM offers 3-, 5-, and 7-axis centers, as well as single-source capability. EPTAM Precision Plastics also offers complete fabricating capabilities for CNC turning, Swiss, milling, routing, sawing, and drilling.
Okuma M560-vertical mill
- 15K RPM spindle
- 32-tool magazine
- Max machining volume: 41”x22”x18”
- Thermal displacement compensation
Okuma MU-4000V 5-axis CNC vertical mill
- 15K RPM spindle
- 32-tool magazine
- Max machining volume: 29”x18”x18”
- Thermal displacement compensation
Okuma L3000 lathe
- 12-station turret
- Max turning diameter: 13.4”
- Max turning length: 19.69”
Okuma M560-vertical mill
- 15K RPM spindle
- 32-tool magazine
- Max machining volume: 41”x22”x18”
- Thermal displacement compensation
Okuma MU-4000V 5-axis CNC vertical mill
- 15K RPM spindle
- 32-tool magazine
- Max machining volume: 29”x18”x18”
- Thermal displacement compensation
Okuma L3000 lathe
- 12-station turret
- Max turning diameter: 13.4”
- Max turning length: 19.69”
Okuma LT2000 EX lathe
- Twin spindle
- 16-station turret
- Max turning diameter: 8.27”
- Max turning length: 5.12”
Okuma Multus B300 mill/turn
- Multi-tasking mill/turn combination
- 6k RPM milling spindle
- 60-tool magazine
- Max turning diameter: 24.8”
- Thermal displacement compensation
Okuma MA-600H horizontal mill
- 10K RPM spindle
- 60-tool magazine
- Max machining volume: 41”x35”x39”
- Thermal displacement compensation
Okuma LT2000 EX lathe
- Twin spindle
- 16-station turret
- Max turning diameter: 8.27”
- Max turning length: 5.12”
Okuma Multus B300 mill/turn
- Multi-tasking mill/turn combination
- 6k RPM milling spindle
- 60-tool magazine
- Max turning diameter: 24.8”
- Thermal displacement compensation
Okuma MA-600H horizontal mill
- 10K RPM spindle
- 60-tool magazine
- Max machining volume: 41”x35”x39”
- Thermal displacement compensation
"Our competitors may all have similar technology, but I believe that our team and culture are differentiators and the reason why our customers choose us to partner with on their critical projects."
Kevin Welch
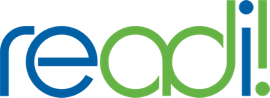
Rapid Prototyping
Every EPTAM client faces the same challenges – design parts to meet performance standards and ensure production ramp and capacity availability while controlling costs.